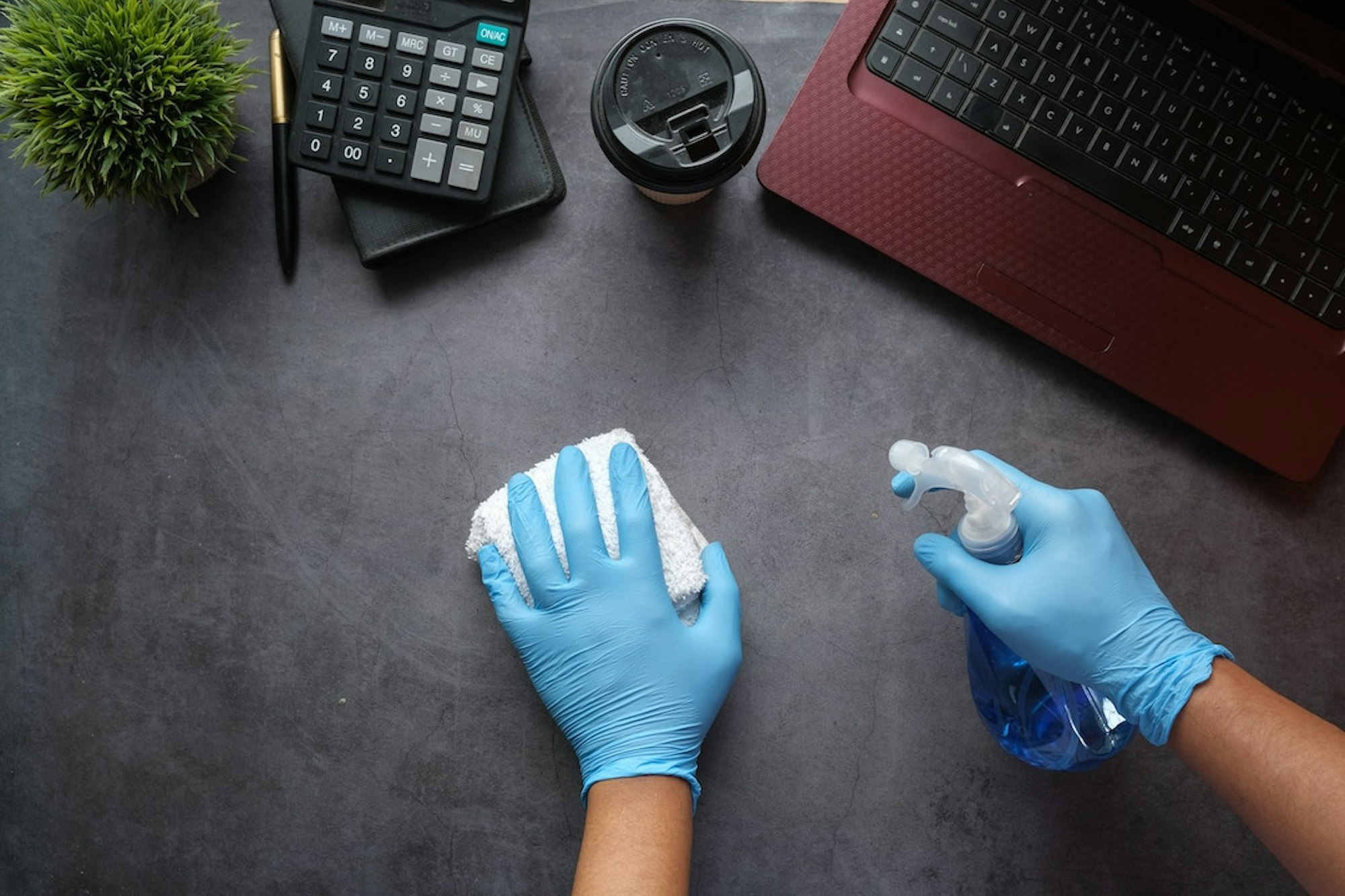
3 Common Mistakes to Avoid When Cleaning Commercial Facilities
- 5 min read
- Castle
The commercial cleaning industry has a significant impact on public health, the environment, and the overall reputation of businesses. Any mistakes in cleaning practices can have detrimental consequences, which are both costly and dangerous for all involved.
Therefore, it is extremely important for cleaning companies to ensure their processes are carried out safely and efficiently in order to reduce these risks. In this blog post, we will delve into three of the most common mistakes to avoid when cleaning commercial facilities. By understanding these common mistakes, cleaning professionals and business owners can create safer, healthier, and more sustainable environments that leave a positive impression on both clients and the planet.
Mistake 1: Buying Insufficient or Low-Quality Cleaning Products
It can be very easy for businesses to fall into the trap of buying more affordable products in order to achieve a higher profit – however, when it comes to cleaning supplies for commercial facilities, buying cheap and low-quality products will only lead to higher costs in the long run. Using the wrong cleaning products can have detrimental effects on both the cleanliness of the facility and the longevity of the surfaces being cleaned.
Suppose a commercial facility has a variety of surfaces, including hardwood floors, carpeting, and glass windows. Instead of investing in high-quality, specialized cleaning products for each surface, the cleaning contractor opts for a generic all-purpose cleaner to save costs. Initially, it may seem like a cost-effective solution, but it can lead to several problems:
- Ineffective cleaning: All-purpose cleaners may not have the necessary ingredients or formulation to effectively clean specific surfaces. For instance, using a general cleaner on hardwood floors might leave behind streaks, residue, or even cause damage. As a result, the floors may appear dirty or dull, requiring additional cleaning efforts and more time to achieve satisfactory results.
- Surface damage: Harsh chemicals present in some cleaners can damage delicate surfaces like glass or polished metals. If you use a cleaner with abrasive properties on glass windows, it can lead to scratches or streaks, affecting the overall appearance and requiring costly repairs or replacements. Similarly, using an improper carpet cleaner can cause discolouration, fibre damage, or even shrinkage.
- Increased maintenance costs: Insufficient or low-quality cleaning products can result in surfaces deteriorating more quickly. For example, if you use a cheap floor cleaner that leaves behind a residue, it may attract dirt and grime, making the floors appear dirty even after cleaning. This leads to more frequent cleaning and additional labour costs. Additionally, if these products are less durable, they may need to be replaced more often – costing much more overall than if a company just invested in higher-quality products.
- Poor impression and customer dissatisfaction: Lower quality cleaning can have a negative impact on the overall appearance and hygiene of your facility. If customers or visitors notice dirty or poorly maintained surfaces, it reflects poorly on your business’s image and professionalism. This can lead to a decline in customer satisfaction, negative reviews, and potential loss of business opportunities.
To avoid these issues, it’s crucial to invest in high-quality cleaning products specifically designed for each surface and follow the manufacturer’s instructions and recommendations for proper use. While these products may initially have a higher cost, they will provide better cleaning results, protect surfaces, and save money in the long run by reducing the need for repairs, replacements, and frequent re-cleaning.
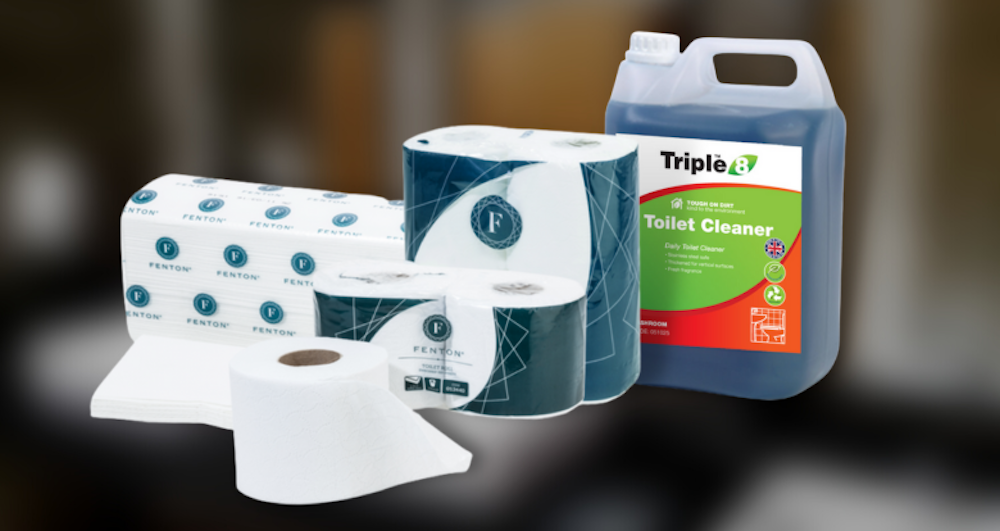
Mistake 2: Neglecting Regulatory Requirements
Cleaning commercial facilities requires adherence to regulations and standards to prioritise safety, environmental protection, and worker well-being. In the United Kingdom, specific regulations should be followed to ensure compliance. Here are some important regulations to be aware of:
- Control of Substances Hazardous to Health (COSHH) Regulations: COSHH regulations aim to protect workers from exposure to hazardous substances. When it comes to cleaning, this regulation is particularly relevant as cleaning products often contain chemicals that can pose health risks if not handled properly. It is crucial to understand and implement COSHH guidelines to ensure the safe use, storage, and disposal of cleaning chemicals. This includes providing appropriate personal protective equipment (PPE) to employees, conducting risk assessments, and providing training on the safe handling and use of cleaning products.
- Colour Coding: The implementation of a colour-coded system for cleaning equipment and materials is crucial for effective hygiene practices. This colour coding system assigns specific colours to different cleaning tasks and areas and enhances cleaning efficiency and reduces the risk of cross-contamination.
- Personal Protective Equipment at Work Regulations 1992: These regulations require employers to assess and provide suitable PPE to employees who may be exposed to risks that cannot be adequately controlled through other means. While not specific to cleaners, these regulations cover the general requirements for PPE across various industries and occupations, including cleaning.

Mistake 3: Not Investing in Regular Training and Development
Inadequate training is a common mistake that can significantly impact the effectiveness and efficiency of cleaning staff. By regularly training cleaning operatives, businesses can ensure staff:
- Are up to date on the latest best practice and safety protocols: This will not only improve the overall quality of cleaning but also enhance worker safety and efficiency.
- Have complete product knowledge: Training programs provide cleaners with detailed information about cleaning products and their appropriate usage. They learn about different types of cleaning agents, their properties, and the surfaces they are suitable for. This knowledge helps cleaners select the right products for specific tasks and use them correctly to ensure effective cleaning while minimising potential damage to surfaces.
- Are familiar with all equipment: cleaning staff may encounter various types of equipment, ranging from vacuum cleaners and floor polishers to specialised tools for window cleaning or carpet maintenance. Through training, cleaners gain familiarity with different types of equipment, learn how to operate them safely and understand maintenance procedures. This knowledge ensures that equipment is used effectively, reducing the risk of accidents, and extending the lifespan of the tools.
Castle’s product training recommendation: MyTraining
MyTraining is a simple way to deliver bite-size training to cleaning staff! This platform offers:
– Industry-leading recognised practices to uphold standards.
– Ways to keep staff motivated and following the latest good practices.
– Automated record keeping.
– A simple and easy-to-use portal.
– An easy-to-manage monthly subscription.
With MyTraining, businesses can save money on their processes, ensure all staff are proficiently trained according to the latest industry and product usage standards, and encourage a more sustainable work culture.
For More Industry Tips, or to Buy Cleaning and Hygiene Supplies, Talk to Castle (EU)
At Castle (EU), everything we do revolves around making your lives easier. Our sustainable cleaning products, staff training, and product supply facilities are designed to help you run your cleaning contracts safely and efficiently – without it costing you the earth!
Whether you’re just starting out in the cleaning industry or looking to take your business to the next level, we’re here to help. Contact our team today for more information on how we can support your needs.